传统钣金工艺的困境:效率与精度如何兼得?
在钣金加工领域,手工绘图、经验估算和反复试错曾是行业常态。一位从业二十年的老师傅坦言:“一个复杂的异径三通展开图,手工计算至少半天,稍不留神还会因尺寸误差导致材料报废。”随着市场竞争加剧和客户需求多元化,传统工艺的效率瓶颈和精度风险日益凸显——企业如何在保证质量的前提下,将交付周期缩短30%?又如何应对小批量定制化订单的灵活需求?金林钣金软件智能高效革新钣金工艺首选利器的诞生,为这些争议性问题提供了突破性答案。
1. 效率提升:从半天到5分钟,可能吗?
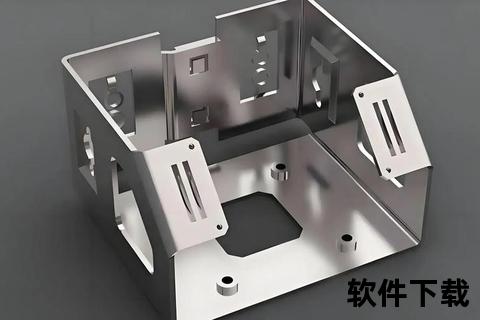
以某机械制造企业的真实案例为例:该企业承接了一批变径锥管订单,传统工艺下,技术员需手动计算锥管展开图的弧长、弦长等参数,耗时长达4小时,且因板材厚度处理不当导致5%的废品率。引入金林钣金软件智能高效革新钣金工艺首选利器后,技术员仅需输入锥管大端内径(d1=600mm)、小端内径(d2=360mm)和偏心距(S=50mm)等参数,软件5分钟内自动生成带板厚补偿的展开图,并通过AutoCAD直接输出加工文件。数据显示,该企业生产效率提升30%,材料浪费率降至1%以下。
软件的核心优势在于其覆盖7大类、120余种钣金构件的数据库,例如圆管弯头、方圆过渡管等,每类构件支持参数化调整,如直径、角度、偏心量的动态输入范围验证功能(如要求h1≥S以避免阻力过大),确保设计即合理。这种“输入即生产”的模式,彻底改变了传统工艺的线性工作流。
2. 多样化需求:一套软件能否通吃行业痛点?
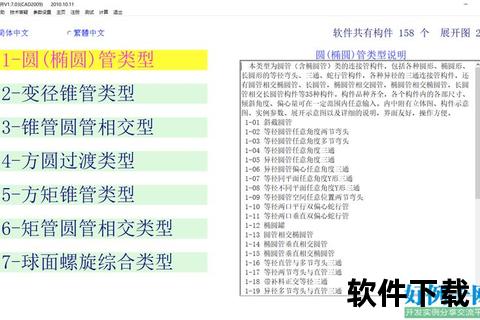
钣金加工的复杂性体现在构件类型的多样性上。某汽车零部件制造商曾面临难题:同一生产线需处理圆管与四棱锥管相交、球面螺旋叶片等特殊构件,传统软件无法兼容不同结构的展开计算。金林钣金软件智能高效革新钣金工艺首选利器通过模块化设计解决了这一痛点:
模块协同:在“矩管圆管相交类型”中,软件自动校验圆管中线与锥管边的高度关系(h2>d3/(2cosα)),避免干涉;
工艺融合:对于不可展曲面(如球罐),软件提供经线法、纬线法两种近似展开方案,并通过弦长截取算法(Rc(1)~Rc(n/2+1)半径画弧)控制误差在0.5mm内。
某高端家居定制企业借助软件的“上圆斜下矩平偏心连接管”模块,实现双偏心圆矩连接管的精准放样,使定制化订单交付周期缩短15%,客户满意度提升40%。
3. 智能化升级:如何从工具到生产中枢?
金林软件的智能化不仅停留在设计层面,更延伸至生产全流程。以某钣金工厂的数字化改造为例:
数据贯通:软件输出的DXF文件直接对接激光切割机,消除人工转录误差;
版本管控:通过中央服务器存储展开图,避免技术员电脑、邮件、U盘等多版本混乱(此前因版本错误导致的废品率高达8%);
成本优化:在“方矩锥管类型”中,软件通过三角形法排版计算,将板材利用率从78%提升至92%,年节约材料成本超50万元。
更值得关注的是,软件支持A0-A4图幅自适应输出,并与ERP系统集成,实现订单参数自动解析、工艺库智能匹配。某上市公司利用该功能,将新品研发到量产的周期从45天压缩至28天。
钣金企业的转型路线图
对于计划引入金林钣金软件智能高效革新钣金工艺首选利器的企业,建议分三步走:
1. 痛点筛查:优先解决高频、高损环节,如异形管件展开(占企业成本的25%以上);
2. 人才储备:组织技术团队学习软件的参数校验规则(如d1>d2>0的锥管输入逻辑),并结合企业产品特点建立专属构件模板库;
3. 系统融合:逐步对接MES、PLM系统,构建从设计到质检的数字化闭环。
在工业4.0浪潮下,钣金加工的竞争已从“设备精度”转向“数据精度”。金林软件通过将老师傅的经验转化为算法,让每一块钢板都能在数字世界中找到最优解——这或许正是传统制造业破局的关键。