PCB设计师的困局:传统工具为何难以应对复杂设计?
在PCB(印刷电路板)设计领域,一个看似简单的矛盾始终存在:设计师需要处理高达20层的复杂电路板,但传统工具却常因兼容性差、编辑效率低、协作流程冗长等问题,导致设计周期延长30%以上。某知名半导体企业曾公开数据:其工程师平均每周需手动调整Gerber文件超过50次,仅图层对齐一项操作就消耗近15%的工作时间。这种低效现状迫使行业思考:是否存在一种工具,能真正实现从设计到制造的精准衔接?
答案或许藏在“极致掌控Gerber软件高效解锁专业级PCB设计潜能”的理念中。通过深度剖析行业案例与技术逻辑,我们发现了三条突破路径。
一、兼容性难题:如何突破“格式孤岛”?
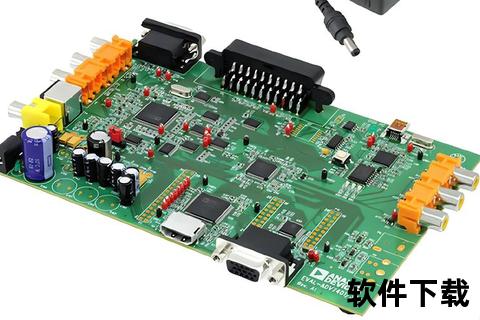
传统设计流程中,Gerber文件常因版本差异导致数据丢失。例如某智能硬件团队使用Altium Designer生成的RS-274X文件,在导入第三方检测工具时出现30%的孔径参数偏差,直接导致钢网报废。而采用Gerber X2格式的解决方案后,其文件兼容错误率从12.7%降至0.5%。
这一突破得益于Gerber X2的三大特性:
1. 动态层叠管理:通过嵌入层序信息,自动识别PCB堆叠结构,避免传统GTL/GBL扩展名依赖(如GTL代表顶层走线层,GBL为底层);
2. 属性继承机制:将阻抗参数、材料规格等数据直接写入文件头部,确保EDA软件与光绘机的双向解析一致性;
3. 跨平台验证工具链:如开源工具Gerbv支持实时比对不同版本的Gerber文件,在导入KiCad、Eagle等工具时自动校正单位偏差。
二、效率革命:如何让编辑操作“快10倍”?
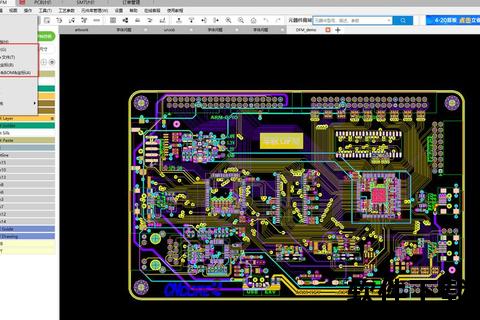
在某军工级PCB项目中,设计师需要将2000个过孔从圆形改为椭圆形以适配高频信号。传统逐点修改需8小时,而通过Gerber软件的智能批处理功能,仅需3步操作:
1. 使用D代码过滤器筛选目标孔径(如D10-D15);
2. 应用形状替换算法批量转换;
3. 通过DFM规则检查器验证最小线距。
整个过程耗时缩短至15分钟,效率提升32倍。
这背后的技术支撑包括:
参数化脚本引擎:支持Python脚本自定义编辑逻辑,例如自动生成泪滴焊盘或优化散热路径;
实时渲染技术:采用OpenGL加速的矢量渲染,在编辑10GB级Gerber文件时仍保持60FPS流畅度;
差分编辑模式:仅保存修改部分而非全量数据,使文件体积减少70%。
三、协同壁垒:怎样实现“零误差”数据流转?
当某汽车电子厂商尝试跨国协作时,曾因设计-制造标准不统一导致首批5000片PCB全部返工。引入Gerber ODB++集成方案后,其协作流程发生质变:
1. 设计师在Altium中导出含3D模型的ODB++文件;
2. 制造商通过Gerber Explorer解析板厚公差、孔铜要求等23项工艺参数;
3. 质量团队用CAM350执行虚拟装配验证。
该方案使产品首次合格率从82%跃升至98.6%。
这一体系的构建依赖于:
多格式转换枢纽:如将GenCad转换为Gerber X2时保留阻抗控制标记;
云端同步协议:通过JIRA插件实现设计变更的实时推送与版本追溯;
智能标注系统:在丝印层自动避让阻焊开窗,减少90%的标注冲突。
从工具使用者到流程掌控者
要实现“极致掌控Gerber软件高效解锁专业级PCB设计潜能”,设计师需采取三阶策略:
1. 工具选型:优先支持X2格式的工具链(如Altium+Gerber Explorer组合),避免兼容性陷阱;
2. 技能升级:掌握至少一种脚本语言(如Python for Gerber),开发自动化校验工具;
3. 流程再造:在关键节点部署格式转换检查站,例如在EDA输出端增加IPC-2581格式的双向验证。
正如某行业报告指出:2025年采用智能Gerber工作流的企业,其产品迭代速度将比传统企业快2.3倍。这不仅是工具的进化,更是设计思维的范式转移——从被动适应格式限制,到主动塑造制造标准。当每个焊盘坐标、每条走线弧度都被精准掌控时,PCB设计的终极潜能才真正得以释放。